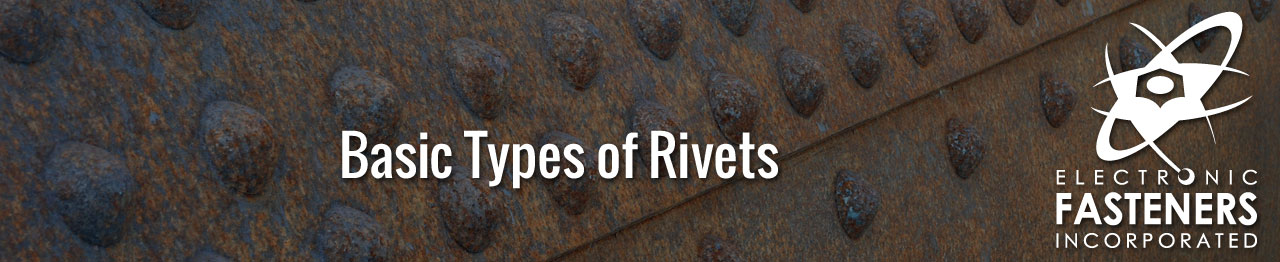
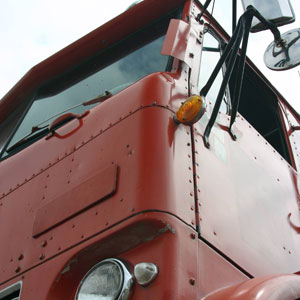
What makes rivets different from most fasteners is that they are permanent. Once installed, they’re not coming off unless they are destroyed in the process. Installation is fairly simple – holes are punched or drilled in the materials being fastened, the rivet is inserted and the smaller end is deformed by impact to flatten it and secure the two pieces tightly together. The original head is called the factory head, while the freshly deformed head is referred to as the shop-head or buck-tail.
There are a number of rivet styles designed to suit a wide range of applications, materials, and strengths. Here are the major types used in most applications:
Solid/round head rivets
The original rivet design, going back to the Bronze Age. Solid rivets can be deformed simply with a hammer, a crimping tool, or a rivet gun, depending on size and material softness. One of the most reliable, safe, and foolproof rivets around.
High strength/structural steel rivets
Structural steel rivets have been in use for hundreds of years and have been the main rivet for fastening metal structures, such as buildings, ships, and aircraft. While remarkably strong, they require several skilled workers to install, and must be heated immediately prior to use to make them soft enough to deform.
Semi-tubular rivets
Semi-tubular, or tubular, rivets feature an indentation or hole in the end opposite the factory head, making it easier to deform, using less force. Semi-tubular rivets are popular for mass production applications.
Blind rivets
Blind rivets are a tubular rivet known more commonly as pop rivets. Available in a flat head, countersunk head, or modified flush head, blind rivets feature a mandrel that is drawn into the rivet, expanding the blind end and then snapping off to finish securing the connection. Blind rivets are ideal for applications in which the joint can be accessed from only one side.
Oscar rivets
Oscar rivets similar in both appearance and installation to blind rivets, oscar rivets differ in that when the mandrel is drawn through the rivet, the shaft splits and folds out similar to a toggle bolt used to secure things to drywall.
Drive rivets
Drive rivets are yet another form of the blind rivet, with a short mandrel that protrudes from the head and is flared using a hammer. Drive rivets are used in applications where the hole does not penetrate the entire sheet, panel or block (blind holes). Once inserted, the rivet is struck, causing the installed end to expand and grip the side of the hole. Common applications include attaching name plates to objects.
Flush rivets
Flush rivets are best suited for tasks that require an attractive appearance, such as finished metal surfaces where they offer minimal visibility. Because they use a countersunk hole, they present a flush appearance that is also well-suited for aircraft components where aerodynamics are a major concern.
Friction-lock rivets
Similar to an expanding bold, the friction-lock rivet shaft snaps off under tension to help create a flush finish, which has made them another popular rivet for aircraft construction.
Self-pierce rivets
Self-pierce rivets do not require a hole for installation. Instead, the self-pierce rivet features an end that is designed to be punched through top sheet materials into the bottom sheet where a die used with the rivet setter creates a small pocket into which the end expands, holding it in place.