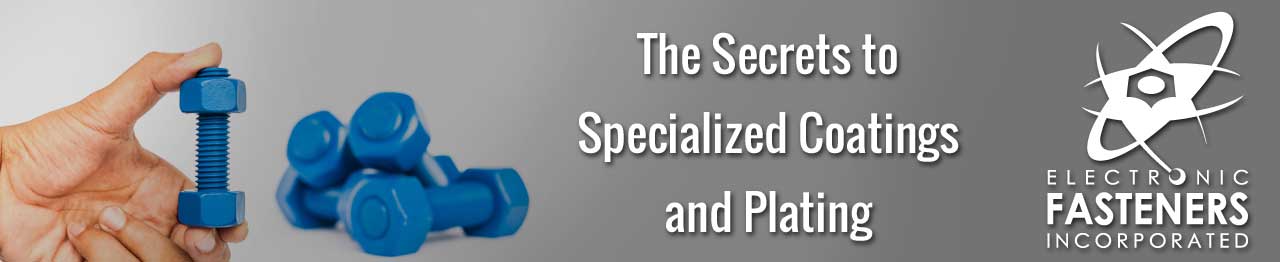
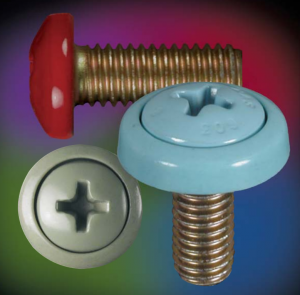
There are a number of different specialized coatings. Here’s a partial list of some of the more popular ones:
Functional Epoxy Offers excellent corrosion protection and electrical insulation properties; typically used on auto alternators and electric motors.
Thin Film Epoxy A visually attractive and durable coating, thin film epoxies are used mostly for indoor coatings because when exposed to long periods of sunlight, it might produce a chalky color.
Urethane Polyester Gives excellent thin film appearance while still withstanding ultraviolet rays. Generally used on garden equipment, office equipment, trailers, and light fixtures.
Polyester TGIC Provides excellent gloss and durability while maintaining edge coverage, along with chemical and impact resistance.
Acrylic – Provides excellent exterior gloss retention, as well as good thin film appearance and chemical resistance. Acrylic was originally used for appliance industry applications.
Epoxy/Polyester Hybrid – Great chemical and corrosion resistance, although lacking in color retention. Used for water heaters, power tools, and shelving.
Plating is an entirely different process that involves creating an outer coating of nickel, copper, chromium or other metal to inhibit corrosion or to enhance the appearance of the parent metal and produce a protective or cosmetic finish. There are several plating methods and many variations of them, including electroplating, vapor disposition under vacuum, and sputter deposition.
Specialized plating can include:
- Gold
- Silver
- Electroless RoHS and Standard
- Chromate Conversion Coating
- Copper
- Nickel
- Rhodium
- Passivation
Coating and plating are processes that require great skill and knowledge to avoid compromising the product that is being coated or plated. The secret is knowing which coater or plater is right for the type of product and metal being finished and the material and process being used to do it. At Electronic Fasteners, we work with a number of highly experienced and reliable platers and coaters who can meet a wide range of commercial and military specifications. To learn more about specialized coating and plating, contact the finishing experts at Electronic Fasteners.