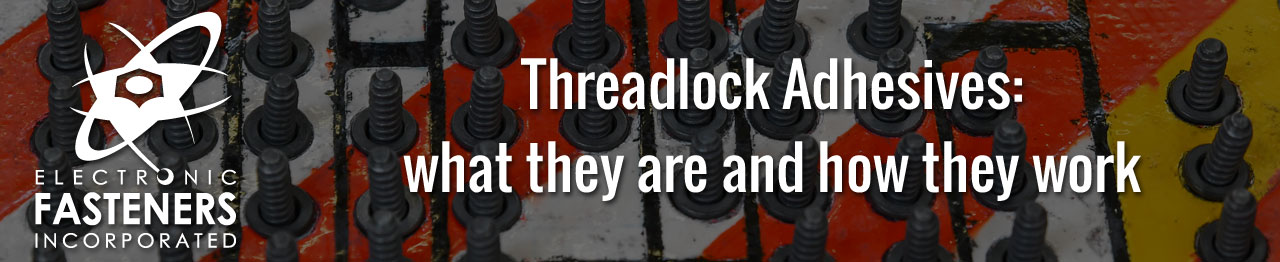
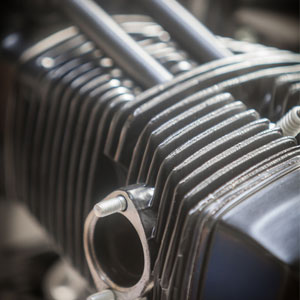
To help prevent tension relaxation and self-loosening, chemical threadlocking adhesives were created almost fifty years ago prevent the two major causes of threaded fastener failure:
- Tension relaxation from changes in temperature that can cause fasteners to expand and contract, loosening in the process
- Self-loosening caused by a lateral sliding motion between fastener contact surfaces, often from vibration, such as moving machinery
Threadlocking adhesives are highly reliable, low-cost materials that boost torque control, reduce wear between the adhered surfaces and provide lubrication to help during assembly. These adhesives will hold critical clamp load pressures even in the most severe environments and offer high shear strength, good temperature resistance, rapid cure, easy dispensing and good vibration resistance.
Threadlocking adhesives come in two formulas: permanent, a heavy-duty adhesive which can withstand up to 3000psi in shear; and removable, which loosen when heat is applied. These adhesives are primarily liquid resins that have anaerobic properties – in the absence of air, they harden to a solid when exposed to metal ions. This unique property enables the adhesive to easily flow and settle into threaded fastener grooves before solidifying. If there is air present, such as on the surface of the material being fastened, any excess liquid resin can be easily wiped up.
The liquid threadlock resin fills any microscopic gap and imperfection in the fastener threads and helps the fastener threads bond with the rough metal surface of the materials being held together, positively locking and sealing the threaded assemblies. The adhesive compound not only prevents lateral motion and fastener loosening, it also helps prevent corrosion by blocking fluids, gasses, and general moisture. Another key benefit of threadlock adhesive use is the 100 percent contact it provides between metal parts, compared to as little as 15 percent in non-treated metal nut and bolt assemblies.
Selecting the right threadlock adhesive
There are several factors to consider when selecting a threadlock adhesive for your application:
- Level of hold
Contrary to popular belief, threadlock adhesives are not permanent. While some are stronger than others, all threadlock adhesives are temporary, allowing fasteners to be removed. Threadlock adhesives are available in three strengths:
-
-
- Low-strength threadlockers are used on screws up to one-quarter-inch in diameter, such as adjustment and calibration screws, meters, gauges and other fasteners that will need ongoing adjustment.
-
-
-
- Medium-strength threadlock adhesives are for fasteners up to three-quarters of an inch in diameter used in machine tools and presses, pumps, compressors, and as mounting bolts.
-
-
-
- High-strength threadlockers are best used on fasteners up to one inch in diameter found in permanent assembly applications such as heavy equipment and a variety of mounts.
-
- Operating conditions
The end-use environment must be taken into account when selecting a threadlock adhesive: temperature range, type of metal surfaces, chemical-resistance, and vibration, to name some of the most common environmental factors.
- Metal type
Fastener metal type can have a major impact on adhesive performance. For example, if two inactive metals are used in the fastener, such as magnesium, zinc, stainless steel, cadmium, black oxide, passivated titanium, or anodized aluminum, a primer may be needed to promote curing. If the fastener contains only one inactive metal, no primer’s needed.
Anaerobic threadlock adhesives in general should not be used with plastic fasteners because they can soften them or create stress cracks.
Applying threadlock adhesive
With the rise in popularity of threadlock adhesives, the use of pre-applied resins by means of manual, semi-automatic, and automatic dispensing systems has increased, enabling manufacturers to reduce waste and cost by applying a specific, consistent amount to fastener components.
Proper application of a threadlock adhesive is critical for ensuring a good hold — the adhesive must be applied to the full length of the fastener and is dependent on thread size, adhesive viscosity, and the geometry of the fastener parts. For large parts, both fastener faces must receive threadlock adhesive to ensure a solid and reliable hold.
Threadlock adhesive should only be applied to the final contact area of nut-and-bolt assemblies after tightening because that is the only area where it’s needed and will cure. Blind-hole assemblies should receive adhesive on both the bolt and the mating threads to prevent the liquid resin from being forced out during assembly which, in turn, would prevent a solid hold.
The future of threadlock adhesives
New adhesive resins are being developed to overcome some of the factors that can negatively affect their efficiency, such as dirty or oily surfaces, high temperatures, vibration, and the need to use primers on some metals. As the efficiency and effectiveness of threadlock adhesives increases, so will their continued popularity.