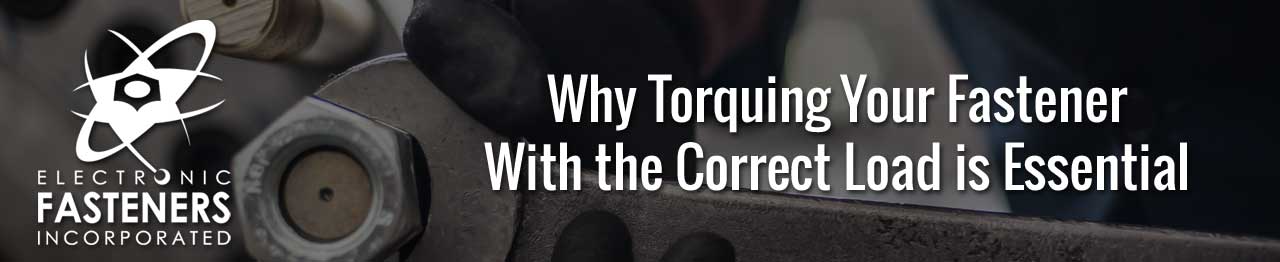
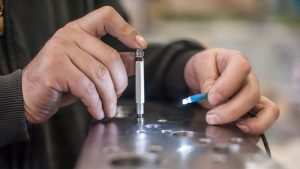
The process of correctly tightening threaded fasteners requires controlling both input torque and angle-of-turn – in fact, there can be as many as 200 or more factors affecting tension when tightening torque is applied to a bolt. Insufficient tightening and the lack of proper preload can lead to premature fastener fatigue and ultimately failure. Even a minimal amount of insufficient torque can result in component movement and cyclic fastener stress that can progress to cracking and a compromised fastener. So for a nut to properly load a bolt and prevent premature failure, the proper amount of torque must be applied, based on a number of variables, including tension and torsion. Both of these are forms of stress – tension is a desired stress, while torsion is undesirable stress caused by friction. Properly applied torque overcomes friction, negating torsion.
Successfully controlling the fastener tightening process requires an understanding of the relationship between torque and turn to develop the right tension. The process of tightening a fastener involves turning, or advancing the threaded fastener, and torque, which produces tension in the fastener.
Torque-and-turn has four distinct, progressive zones of engagement:
- Rundown in which the fastener is turned until the head or nut contacts the bearing surface.
- Alignment in which the fastener and joint mating surfaces are aligned to achieve a snug condition.
- Clamping range in which the slope of the torque-angle curve is essentially constant.
- Post yield zone in which some portion of the components yield slightly to achieve the proper tension.
Regardless of the type of threaded fastener you’re using, applying the correct load to the components enables the fastener to maintain its integrity and function properly. Too much or too little torque can cause premature wear-and-tear or stress fractures and damage the fastener.
To learn more about correct fastener loads and torquing contact the threaded fastener specialists here at Electronic Fasteners.