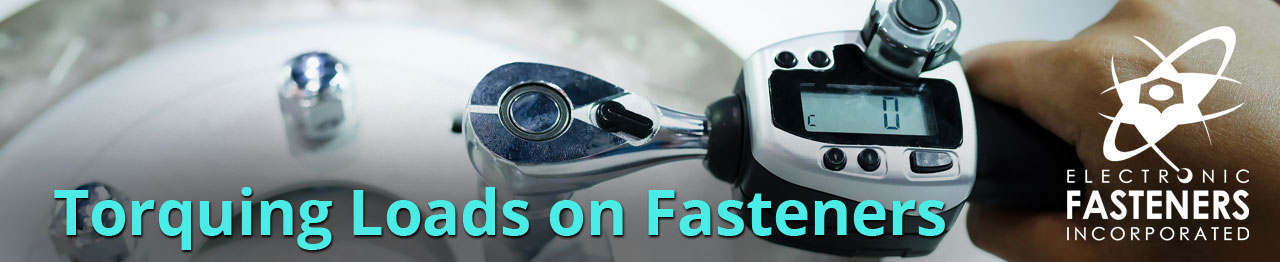
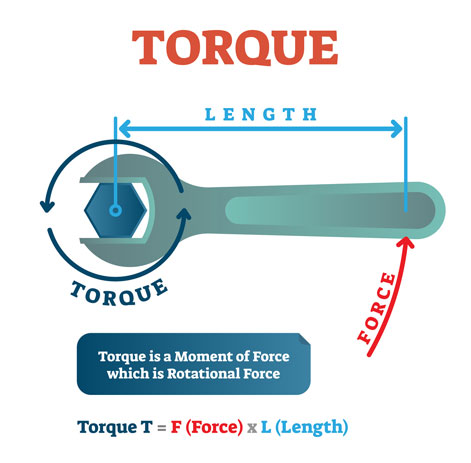
Torque is measured in force multiplied by distance and expressed in foot pounds. Imagine a 2-foot wrench with a 10-pound weight at the end – that’s a torque value of 20 ft lbs on the nut or bolt. In real life applications your hand applies the force and the length of the wrench creates the distance. This is how torque is transferred to a nut or bolt — force multiplied by distance.
Here are three tips to ensure that you apply proper torque for your fastener application:
- Determine torque requirements.
When determining correct torque specifications, consider the maximum load placed on the fastener, the strength of the materials being joined, and whether the joint is hard or soft. Hard joints connect materials directly and fasteners used in them only need to rotate a few degrees to develop full clamping forces once they encounter the material. Soft joints utilize a gasket or compressible materials and require additional tightening to achieve full clamping force after fasteners make contact.One traditional method of determining torque requirements is to destructively test the actual fastener and material being joined. Evaluations are usually conducted with 10 parts, 10 fasteners, and a calibrated torque-control tool with a transducer. First, the fastener is tightened to the point of failure. This is then repeated several times to verify the consistency of the failure point. Another series of tests uses torque to 75% of the failure point. Depending on how parts will be used, the tightening can be reduced by any degree necessary. For example, if parts will experience heavy vibrations, 85% of the total force may be necessary for good torque control. - Pick the right tool.
A wide variety of tools are available to control and measure torque applied to fasteners — they can range from electric screwdrivers to large industrial wrenches and include analyzers, sensors, and multipliers. These tools use calibrated torque-setting mechanisms that may be factory-set or user-definable. After reaching specified settings, the tool gives a visual, audible, or tactile signal.Choosing a tool for a given application is based on the anticipated production output, type of materials being joined, amount of torque required, and specified fasteners. Lighter materials such as wood or plastic may require only lightweight tools. Heavy materials such as steel may require stronger or larger tools. - Use torque analyzers.
Torque analyzers can quickly and reliably calibrate torque tools to their proper settings. They can also be used for quickly testing on the production line or in the quality control lab to determine whether torque tools are holding a given setting. Quality-control inspectors can use them to calibrate torque sensors and verify torque on fasteners. A quality torque analyzer should have enough memory to record several hundred readings, and it should store calibration data for multiple torque sensors.
The importance of proper torque cannot be overestimated. Improperly tightened fasteners affect more than just the joint. Products that contain inefficient or unreliable fasteners create inefficient or unreliable products and that can adversely affect the manufacturer’s reputation and revenue.