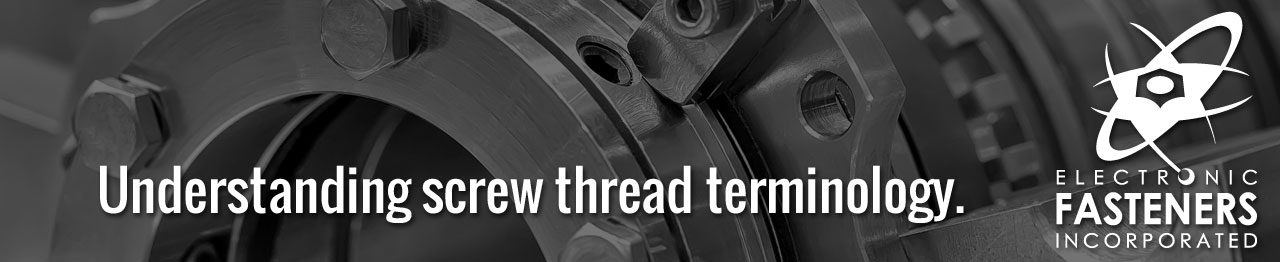
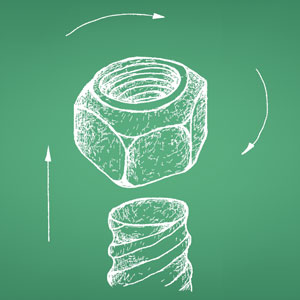
How screw threads are formed
Screw threads are formed by two major processes: rolling and cutting. Rolled threads are formed by squeezing a screw blank between reciprocating serrated dies so that the blank’s metal is squeezed to form ridges with a larger diameter than the unthreaded blank. Cut screw threads are formed using a cutting tool such as a lathe.
Thread classes
Threads are initially identified as either internal (as inside a nut) or external (the outside of a screw), also known as male and female. External threads or bolts are designated with the suffix “A”; internal or nut threads with “B”. Threads are distinguished by the amounts of tolerance and allowance specified; for general guidance, the higher class number the tighter the fit.
Basic screw threads classes and terms:
1A & 1B: For rough commercial quality work where loose fit for spin-on-assembly is desirable
2A & 2B: The recognized normal production standard for the majority of commercial bolts, nuts and screws
3A & 3B: Provides a close fit between mating parts for high quality work
Class 4: An obsolete thread class that was more theoretical than practical
Class 5: Used principally for studs and their mating tapped holes; a force fit requiring the use of a wrench and application of high torque for semi-permanent assembly
Full diameter shank: The major diameter, measured to the outside of the thread and produced by cut thread or by roll thread on an extruded blank
Lead: The distance a screw thread advances in one turn along the screw’s axis
Major diameter: The largest diameter of a screw, measured from the edge of the thread
Minor diameter: The smallest diameter of a screw, measured from the base of the thread
Pitch: The distance from one point on a screw thread to a corresponding point on the next thread, measured parallel to the axis
Pitch diameter: The simple, effective diameter of screw thread, approximately half way between the major and minor diameters
Rolled thread: Threads that are cold-formed by squeezing the screw blank between reciprocating serrated; this acts to increase the major diameter of the thread over the diameter of unthreaded shank (if any), unless an extruded blank is used
Undersized shank: Approximately equal to the pitch diameter of the thread and produced by roll-threading a non-extruded blank