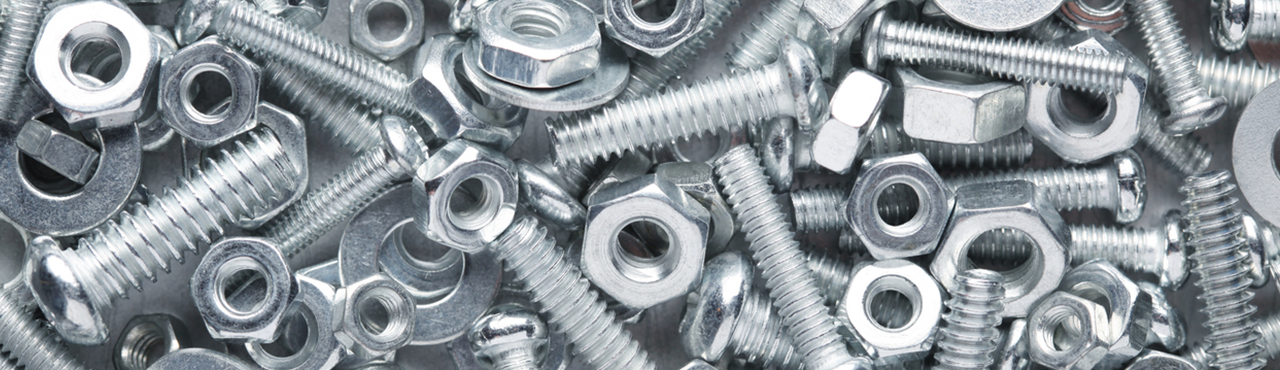
For many companies, inventory control can be a challenge. The goal is to not sit on excess raw material, tying up large amounts of cash and space, but also not run short, halting production and losing time and money. Having the bare minimum amount of inventory to sustain production is the delicate balance of lean supply chain management.
Fortunately, there’s a successful approach to maintaining proper inventory levels based on actual usage and periodic increases or decreases in demand, such as seasonal fluctuations. The cornerstone of this strategy is something called a vendor-managed inventory control system. It’s a business model in which the manufacturer provides a forecast to the supplier of components needed in the manufacturing process, and the supplier takes the responsibility for maintaining an agreed-upon inventory of the item.
Here at Electronic Fasteners, we provide a comprehensive vendor managed inventory (VMI) program in which we set up minimum and maximum product quantities to be maintained for each customer item, based on an item usage report. Each item in our VMI program receives a unique barcode that enables our team of inventory control specialists to check customer inventories for reorder through our inventory management system.
Our VMI program is highly popular with customers who need to refill inventories on a regular basis. It’s a cost-efficient, highly effective system that saves customers time and money while enabling their employees to focus on tasks other than checking, ordering, and restocking items. We even provide regular, real-time usage reports to keep customers apprised of current inventory levels, enabling them to anticipate when and how much additional inventory they may need to order to meet seasonal or contract demands, keeping the flow of needed products uninterrupted and on time to avoid costly production delays.
Your components are stocked at our warehouse, ready to resupply your on-site inventory. We actively monitor your parts status at no extra charge, using bar-coded bins and stocking locations as well as regular inventory management reports that we review with you to ensure the timeliness and accuracy of your inventory supply.
If our VMI program sounds like a good idea for your manufacturing operation, our dedicated VMI department is ready to help you get set up. We’ll design a stocking plan based on your specific inventory needs and deliver your components according to a prearranged plan so that you neither run out of critical parts nor sit on too much inventory, tying up valuable resources.
To learn more about our VMI program and all its benefits, contact our VMI department today.